20th OCT 2023 The PVC WPC Foam Board Extrusion Machine past customer audit.It will be send to Ghana client
Welcome to the factory to watch the test machine!
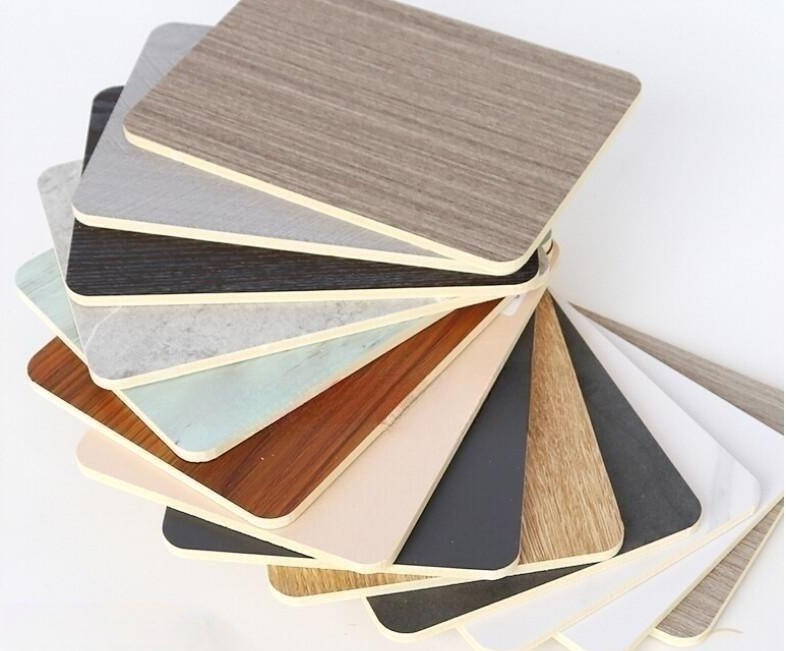
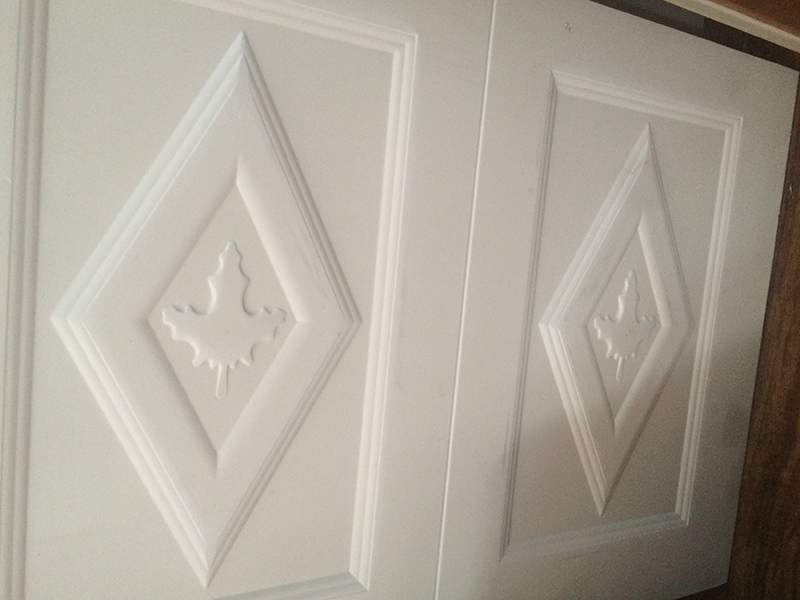
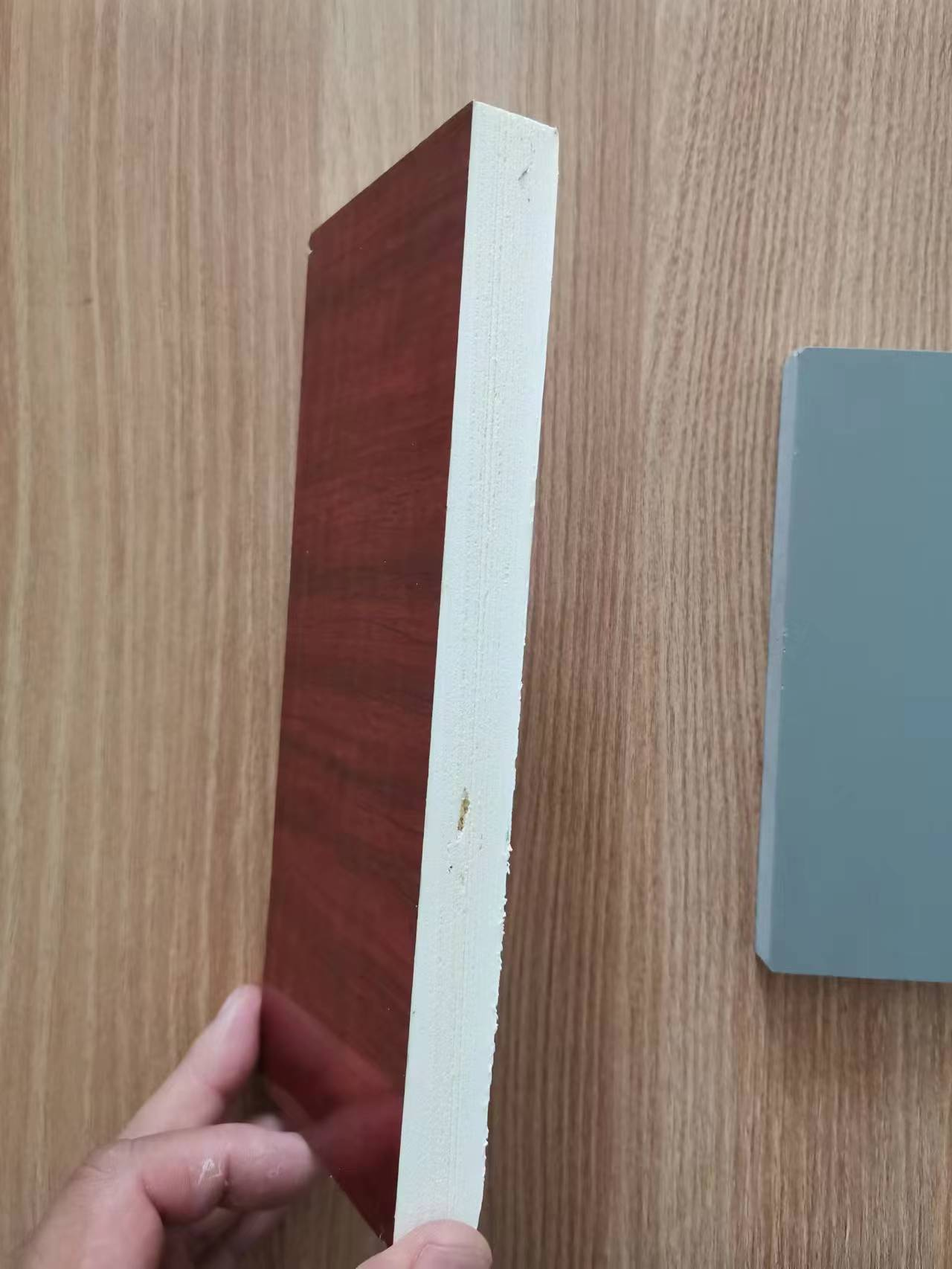
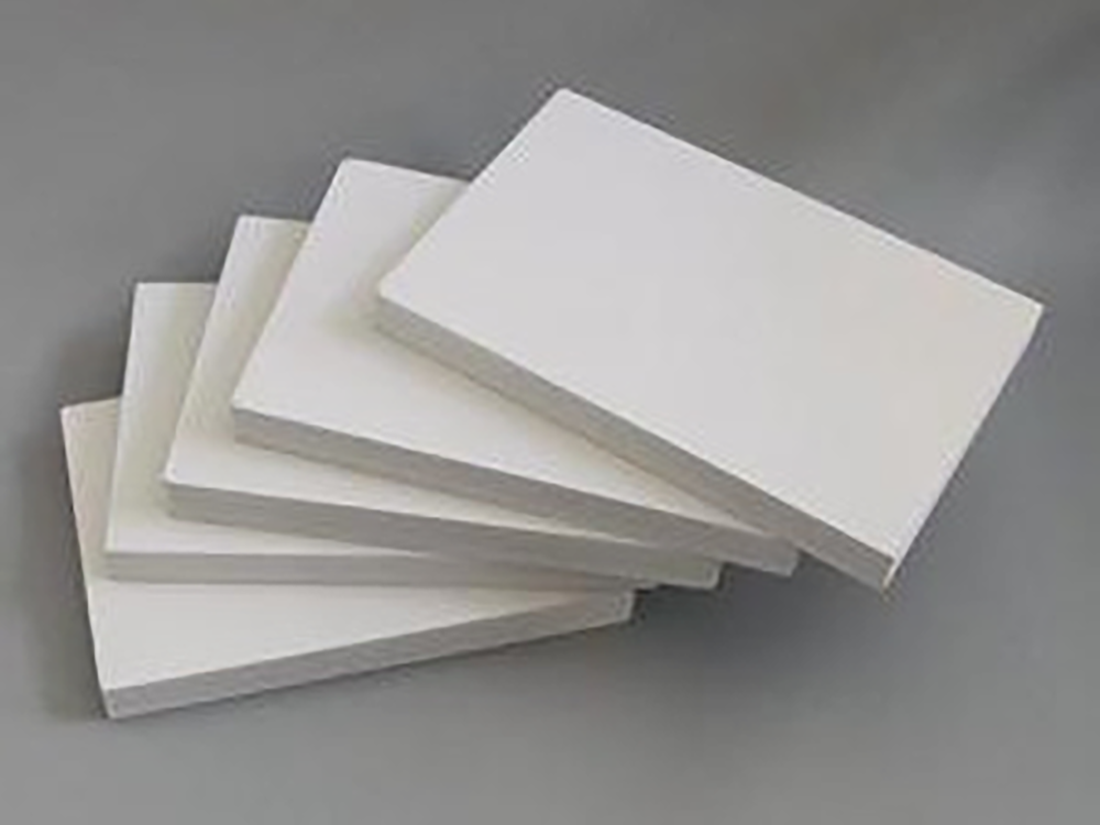
The PVC WPC foam kitchen board extrusion machine
PVC foam kitchen boards are widely used in kitchen interiors for various applications. Here are a few common uses:
Cabinet Doors: PVC foam boards are a popular material for making cabinet doors. They are lightweight, durable, and resistant to moisture and heat. These boards can be easily cut into different shapes and sizes to fit the cabinet frames. Additionally, the smooth surface of PVC foam boards allows for easy cleaning and maintenance.
Backsplash: PVC foam boards can be installed as a kitchen backsplash. They provide a clean and modern look to the kitchen while protecting the walls from splashes and stains. PVC foam boards are available in a wide range of colors and finishes, allowing you to customize the backsplash according to your preferences.
Countertop Trim: PVC foam boards can be used to create decorative trim or edging for kitchen countertops. They can be cut into different profiles and shapes to add a stylish touch to the countertop. The durability and moisture resistance of PVC foam boards make them suitable for this application.
Wall Paneling: PVC foam boards can be used as wall panels in the kitchen to give a contemporary and clean appearance. They can be easily installed and provide a smooth surface that is easy to clean. PVC foam boards are resistant to moisture, making them suitable for kitchen environments.
Shelving: PVC foam boards can be used to create floating shelves or open shelves in the kitchen. They are lightweight yet sturdy, making them ideal for displaying small kitchen items or storing cookbooks.
It is important to note that PVC foam boards should not come into direct contact with open flame or excessive heat as they are not fire-resistant. Additionally, it is advisable to follow the manufacturer's guidelines for proper installation and maintenance of PVC foam kitchen boards.
The advantage of WPC door panel
There are several advantages of using PVC (polyvinyl chloride) kitchen boards:
Durability: PVC kitchen boards are known for their durability and can withstand daily wear and tear. They are resistant to scratches, stains, and water damage, making them suitable for a busy kitchen environment.
Low maintenance: PVC kitchen boards are easy to clean and maintain. They do not require any special cleaning agents and can be easily wiped clean with a mild soap and water solution.
Versatility: PVC kitchen boards come in a variety of colors, patterns, and finishes, allowing you to choose the one that best suits your kitchen decor. They can mimic the look of natural materials like wood or stone, giving your kitchen a stylish and modern appearance.
Cost-effective: PVC kitchen boards are generally less expensive compared to other kitchen materials like solid wood or stone. They offer a cost-effective option without compromising on quality and aesthetic appeal.
Hygienic: PVC kitchen boards are non-porous, meaning they do not absorb liquids or food particles, which helps prevent the growth of bacteria and mold. This makes them a hygienic choice for use in the kitchen.
It is important to note that PVC contains chemicals that can be harmful if not handled properly. It is essential to follow safety guidelines provided by manufacturers and ensure proper ventilation during installation to minimize any potential health risks.
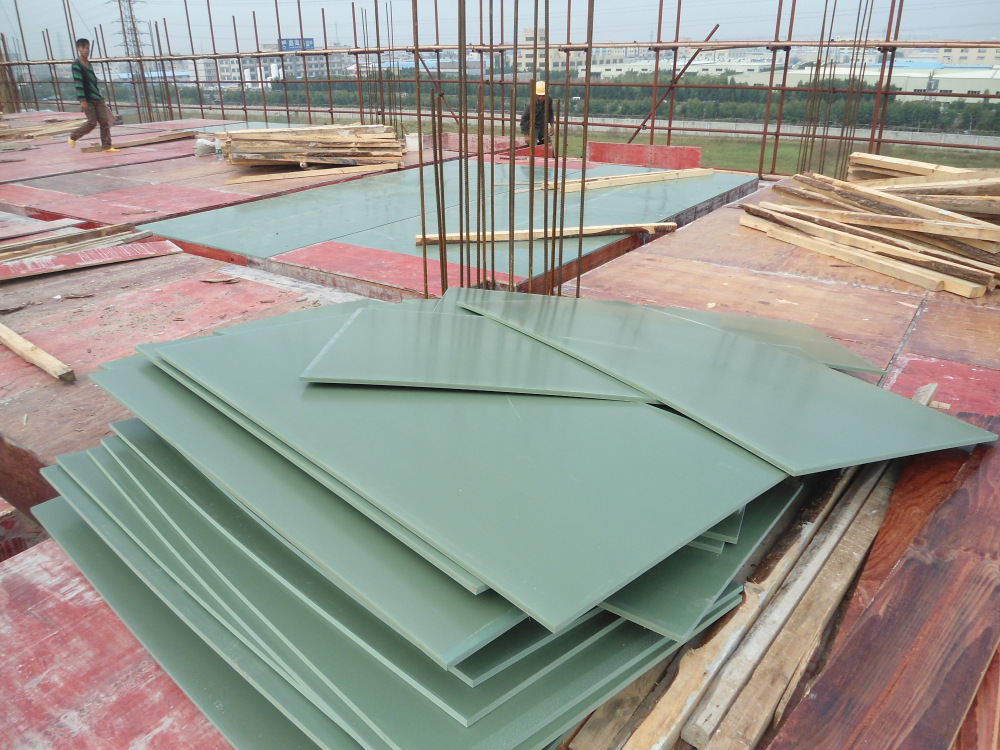
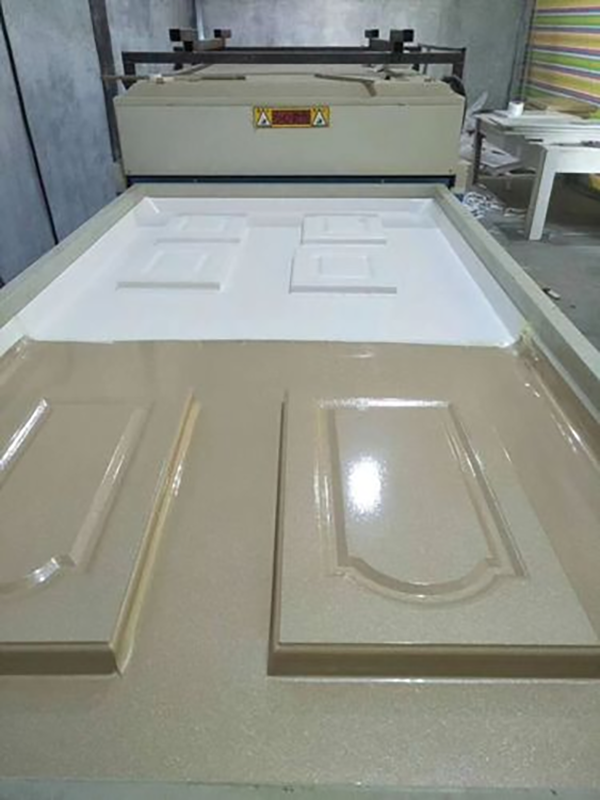
PVC Foam board extrusion machine Flow chart
Here is a flow chart of the PVC foam board machine process:
Raw Material Preparation:
Get raw materials (PVC resin, blowing agent, stabilizers, etc.).
Weigh and mix the raw materials in the appropriate ratios.
Material Loading:
Transfer the mixed materials to the feeding system.
Use a mechanical loader or manual feeding to supply the material to the extruder.
Extrusion:
Material is fed into an extruder, which has a screw and barrel system.
The extruder heats and melts the PVC resin, additives, and blowing agent.
The molten material is forced through a die to obtain the desired shape and thickness.
Cooling and Calibration:
The extruded PVC foam board passes through a cooling tank or calibration table.
Water or cooling air is used to rapidly cool down and solidify the board.
Calibration ensures uniform thickness and a smooth surface.
Cutting and Sizing:
The solidified foam board enters a cutting stage.
It is cut into individual boards of desired lengths using a cutting machine.
The edges may be trimmed to achieve precise dimensions.
Surface Treatment:
The cut boards can undergo additional surface treatment if required.
This may include sanding, embossing, or laminating processes.
Quality Inspection:
Inspect the finished boards for any defects, such as surface imperfections or dimensional irregularities.
Reject any boards that do not meet the required quality standards.
Packaging:
Properly stack and package the inspected PVC foam boards.
Protect them from damage during transportation and storage.
Storage or Distribution:
Store the packaged boards in a suitable warehouse or distribute them to customers.
Please note that the specific flow chart may vary depending on the design and configuration of the PVC foam board machine. This simplified flow chart provides a general overview of the process.
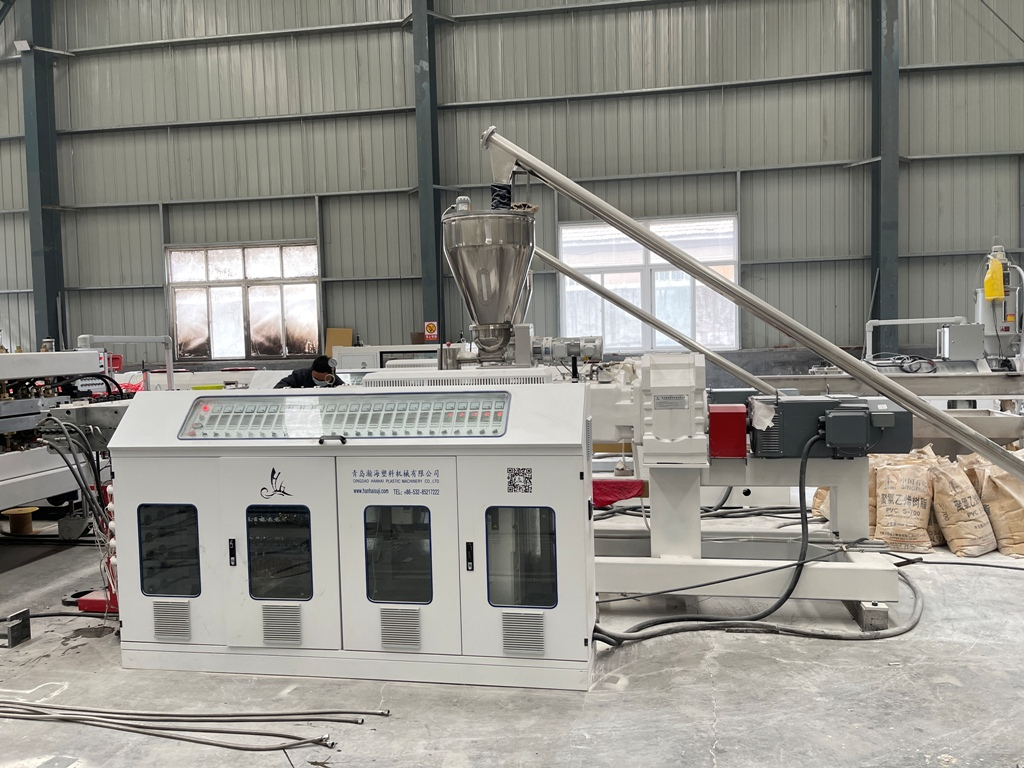
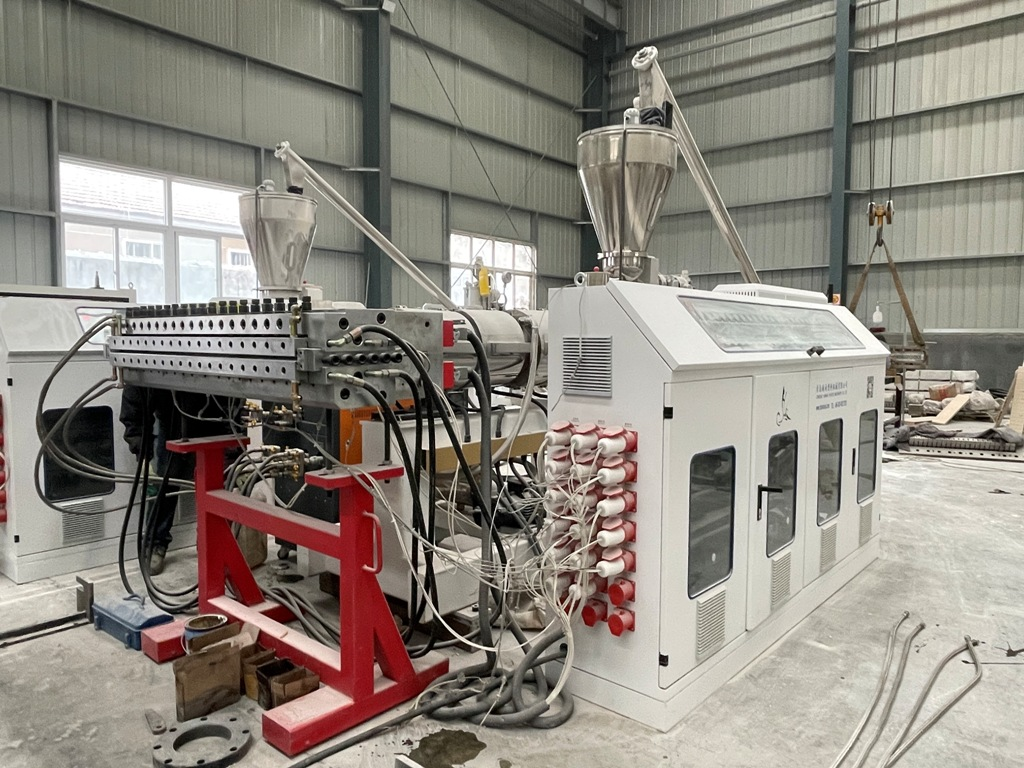
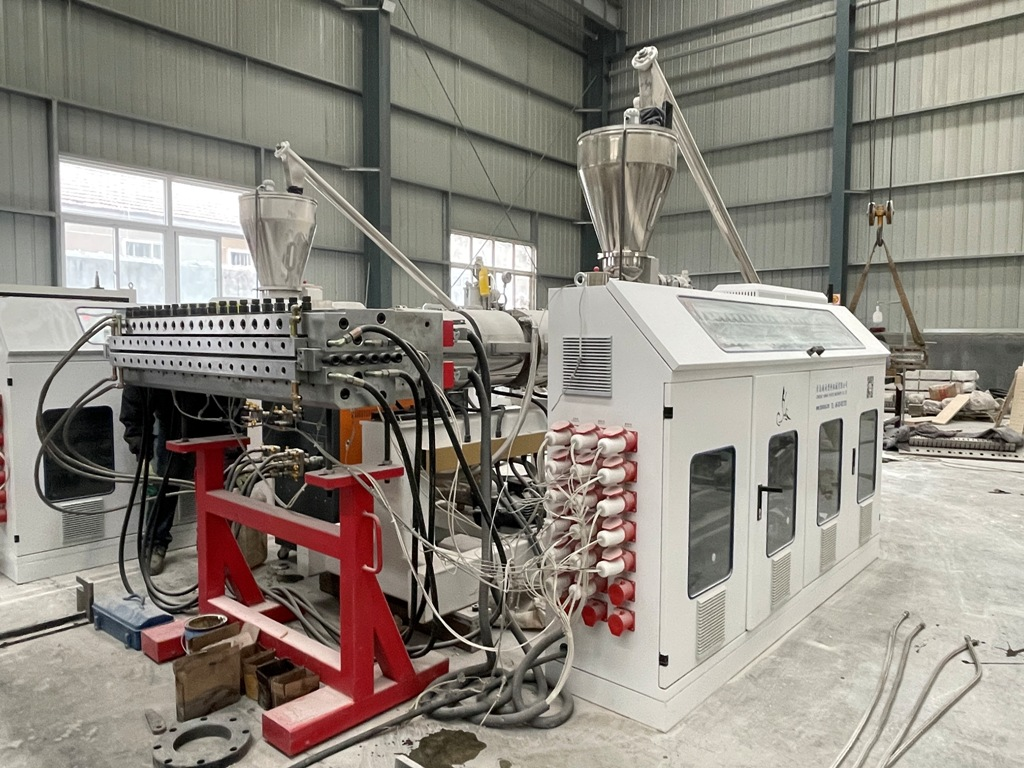
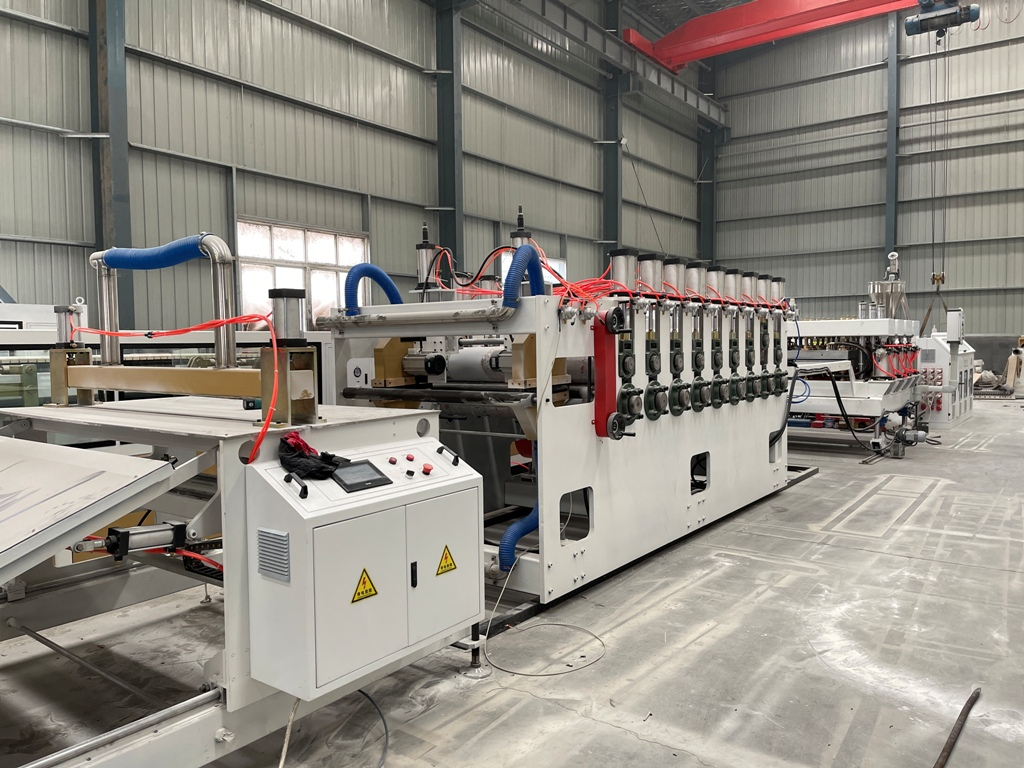
Post time: Nov-20-2023