There are many types of plastic sheets with a wide range of uses. Currently, the main types are polyvinyl chloride, polystyrene and polyester (PET). PET sheet has good performance and meets the national hygiene index requirements for molded products and international environmental protection requirements. They belong to the environmental protection table. Currently, packaging needs to meet environmental protection and recycling requirements, so the demand for PET sheets is getting higher and higher. This article mainly discusses the production process and common problems of PET sheets.
PET sheet production technology:
(1) PET sheet
Like other plastics, the properties of PET sheet are closely related to molecular weight. Molecular weight is determined by intrinsic viscosity. The higher the intrinsic viscosity, the better the physical and chemical properties, but the poor fluidity and difficulty in forming. The lower the intrinsic viscosity, the worse the physical and chemical properties and impact strength. Therefore, the intrinsic viscosity of PET sheet should be 0.8dl/g-0.9dl/g.
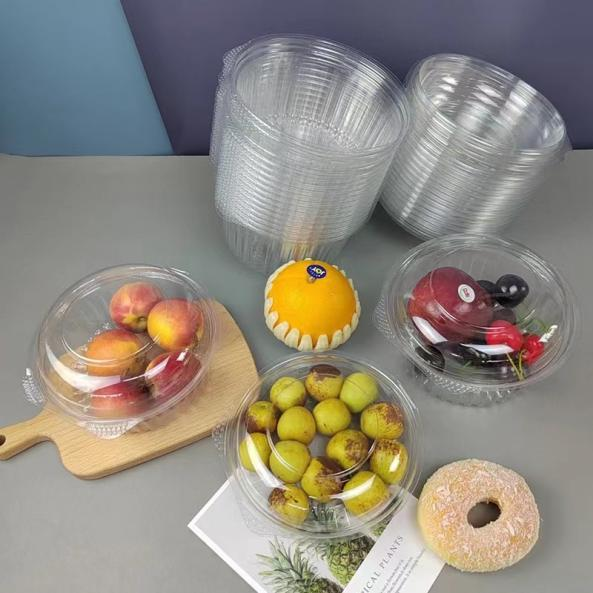
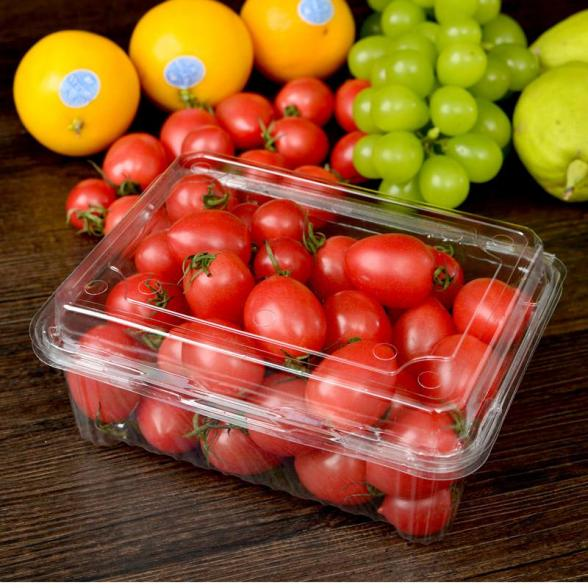
(2) Production process flow
The main production equipment for PET sheets includes crystallization towers, drying towers, extruders, die heads, three-roll calenders and coilers. The production process is: raw material crystallization-drying-extrusion plasticization-extrusion molding-calendering and shaping-winding products.
1. Crystallization. The PET slices are heated and crystallized in the crystallization tower to align the molecules, and then increase the glass transition temperature of the slices to prevent adhesion and clogging of the hopper during the drying process. Crystallization is often an essential step. Crystallization takes 30-90 minutes and the temperature is below 149°C.
2.Dry. At high temperatures, water will hydrolyze and degrade PET, resulting in a reduction in its characteristic adhesion, and its physical properties, especially impact strength, will decrease as the molecular weight decreases. Therefore, before melting and extruding, PET should be dried to reduce the moisture content, which should be less than 0.005%. Dehumidification dryer is used for drying. Due to the hygroscopicity of PET material, when water penetrates deep into the surface of the slice, molecular bonds will be formed, and another part of the water will penetrate deep into the slice, making drying difficult. Therefore, ordinary hot air cannot be used. The hot air dew point is required to be lower than -40C, and the hot air enters the drying hopper through a closed circuit for continuous drying.
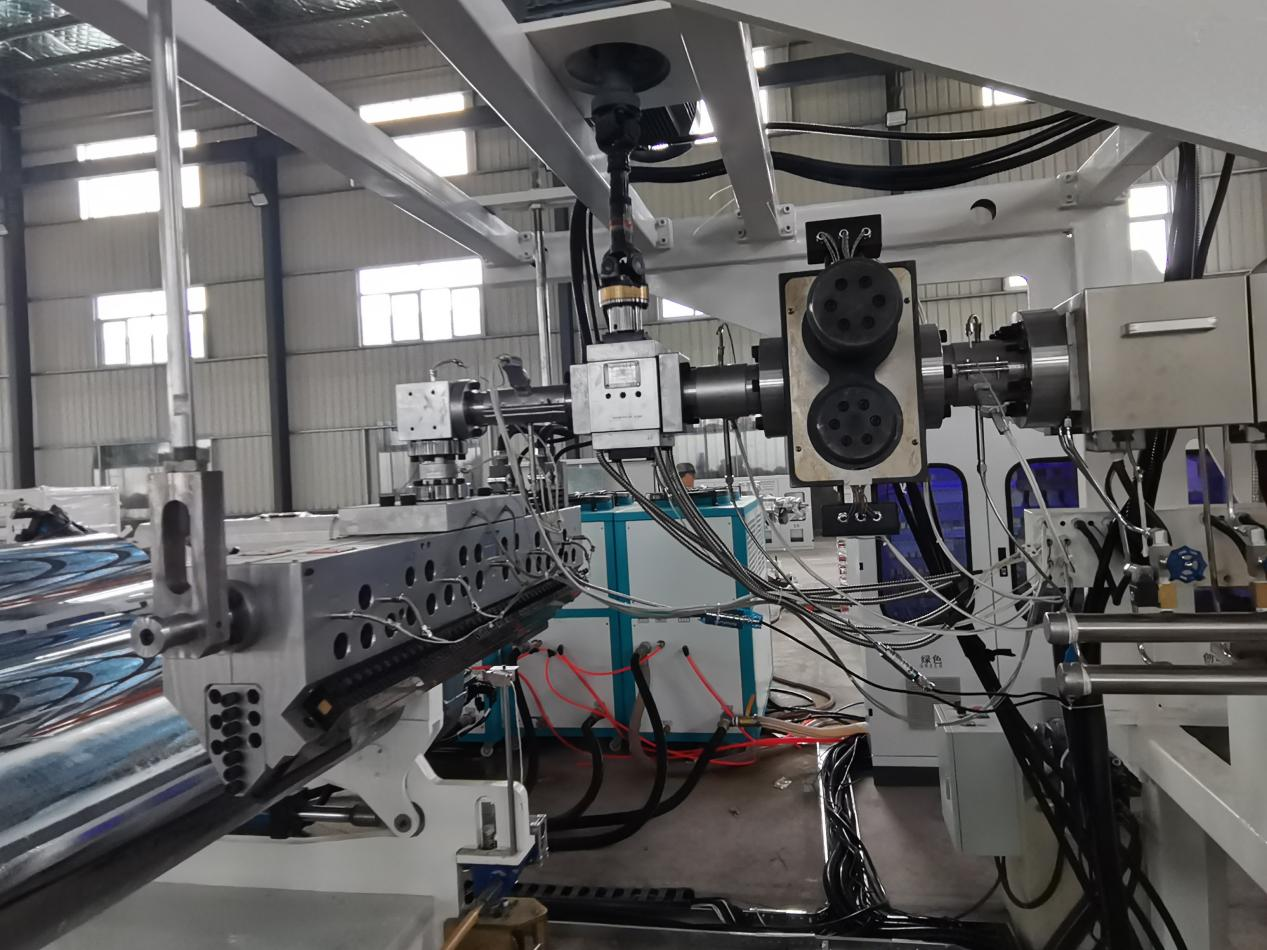
3. Squeeze. After crystallization and drying, PET is transformed into a polymer with an obvious melting point. The polymer molding temperature is high and the temperature control range is narrow. A polyester-specific barrier screw is used to separate unmelted particles from the melt, which helps sustain a longer shear process and increases the output of the extruder. Adopts flexible lip die with streamlined throttle rod. The mold head is tapered. Streamlined runners and scratch-free die lips indicate that the finish should be good. The mold heater has drainage and cleaning functions.
4.Cooling and shaping. After the melt comes out of the head, it directly enters the three-roll calender for calendering and cooling. The distance between the three-roller calender and the machine head is generally kept at about 8cm, because if the distance is too large, the board will easily sag and wrinkle, resulting in poor finish. In addition, due to the long distance, heat dissipation and cooling are slow, and the crystal turns white, which is not conducive to rolling. The three-roller calendering unit consists of upper, middle and lower rollers. The shaft of the middle roller is fixed. During the cooling and calendering process, the roller surface temperature is 40°c-50c. The shaft of the upper and lower rollers can move up and down.
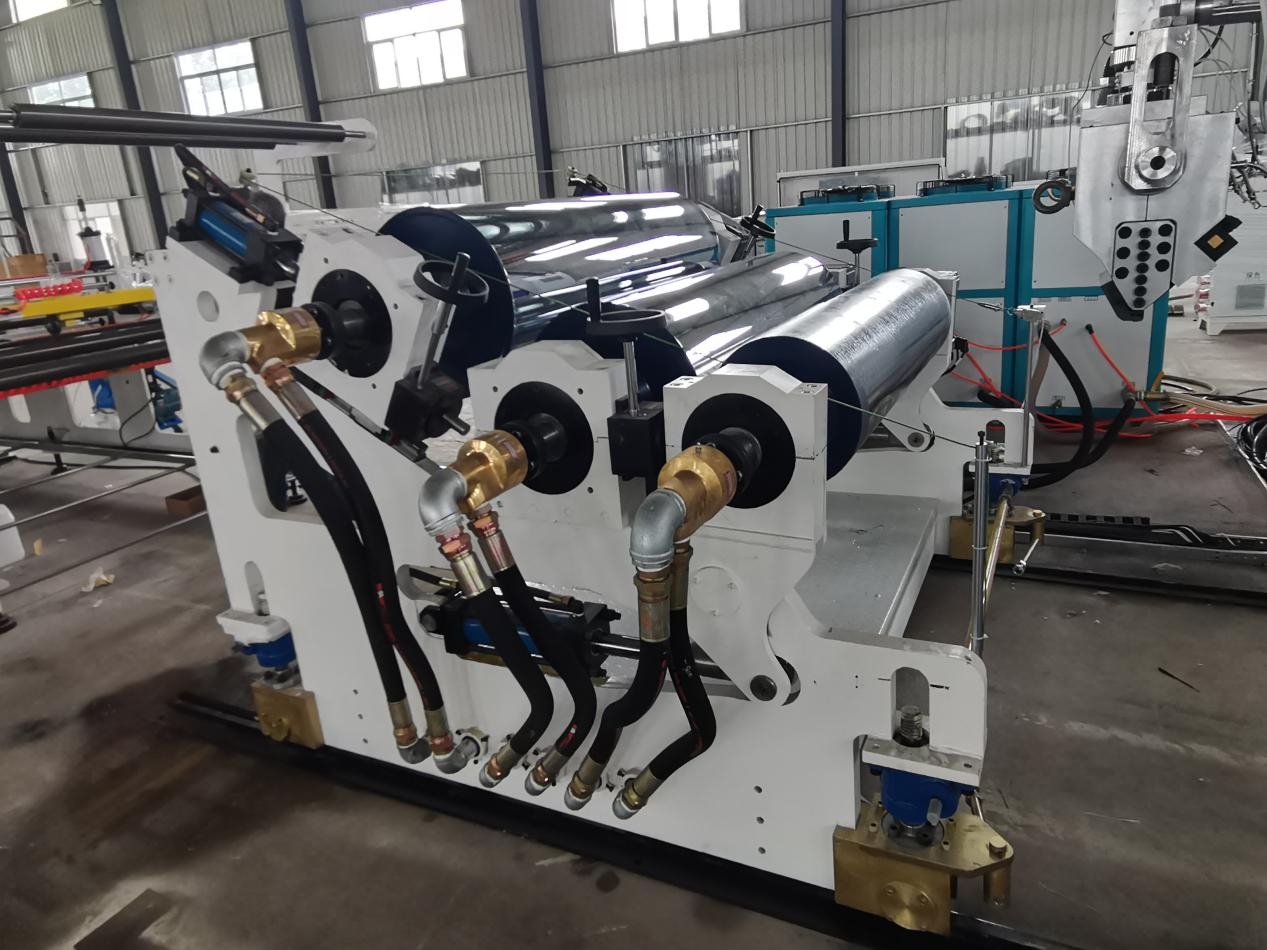
Post time: Sep-28-2023